Precision is the cornerstone of modern manufacturing, especially in industries like aerospace, automotive, medical devices, and electronics, where even the smallest deviation can result in product failure or performance issues. One of the most effective tools for achieving high levels of precision is the lathe, a machine that has been integral to the manufacturing process for centuries. With technological advancements, lathe machining has evolved to play a critical role in producing components with exceptional accuracy. In this article, we will explore how lathe machining enhances precision in manufacturing, from its basic functions to its applications in modern industries.
The Importance of Precision in Manufacturing
Precision in manufacturing refers to the ability to produce parts with exact dimensions and tolerances. In industries like aerospace, medical, and automotive, where components must fit together seamlessly or withstand extreme conditions, precision is paramount. A small misalignment or size discrepancy can lead to malfunction, safety hazards, or costly production errors.
Lathe machining plays a significant role in meeting these precision requirements. The process is particularly well-suited for producing round or cylindrical components, such as shafts, bolts, and bushings, which require tight tolerances to function properly. As technology has advanced, the precision capabilities of lathe machining have improved dramatically, making it an indispensable tool in modern manufacturing.
Lathe Machining
How Lathe Machining Enhances Precision
Consistent Material Removal:
One of the key aspects of lathe machining that enhances precision is the consistency with which material is removed from the workpiece. The rotating motion of the workpiece ensures that the cutting tool can uniformly remove material from all sides. This results in perfectly symmetrical parts, which is critical for applications where balance and uniformity are necessary, such as in rotating machinery parts or engine components.
Controlled Cutting Depth and Speed:
Modern lathes allow operators or automated systems to control the depth and speed of the cutting tool with extreme precision. This level of control minimizes the risk of overcutting or undercutting, which can lead to parts being out of specification. In CNC lathes, cutting parameters such as speed, feed rate, and depth are programmed into the machine, ensuring consistent results from one part to the next. This capability is essential for producing components that meet strict dimensional tolerances, particularly in mass production.
Use of Advanced Tooling Materials:
The cutting tools used in lathe machining have also seen advancements, contributing to higher precision. Carbide, diamond, and ceramic cutting tools are now commonly used in modern lathes due to their ability to maintain sharp edges and resist wear, even during extended use. These materials reduce tool wear, ensuring consistent cutting performance over longer periods and preventing errors due to tool degradation.
Multi-Axis Machining:
In traditional lathes, the cutting tool could move along only two axes: longitudinally (along the length of the workpiece) and radially (toward or away from the center of the workpiece). However, with the advent of multi-axis CNC lathes, cutting tools can now move in additional directions, allowing for more complex geometries and tighter tolerances. Multi-axis machining enhances precision by reducing the need to reposition the workpiece, which could introduce errors. It also allows for the machining of parts with intricate features that would be difficult or impossible to achieve on a standard lathe.
Computer Numerical Control (CNC) Technology:
The introduction of CNC technology has revolutionized lathe machining by automating the process and drastically improving precision. CNC lathes are equipped with computer-controlled systems that follow pre-programmed instructions, known as G-code, to perform the machining operations. This automation reduces the possibility of human error, which is a common issue in manual machining. Additionally, CNC lathes can repeat the same process with extreme consistency, ensuring that each part produced is identical to the others. This is particularly important in industries where large volumes of parts need to be manufactured with tight tolerances, such as in the production of automotive or aerospace components.
Minimal Vibration and Rigidity:
One of the factors that can negatively impact precision in machining is vibration. When a machine or workpiece vibrates, it can cause the cutting tool to chatter, resulting in a rough surface finish and inaccurate dimensions. Modern lathes are designed to minimize vibration through the use of rigid machine structures and advanced damping systems. This stability allows for smoother cutting operations and higher precision, especially when machining hard materials like steel or titanium.
Precision Workholding:
Another critical factor in achieving precision with lathe machining is the way the workpiece is held in place. Modern lathes use advanced workholding techniques, such as precision chucks, collets, and fixtures, to securely grip the workpiece without causing deformation. Proper workholding ensures that the part remains stable during machining, allowing for accurate material removal and consistent results.
Quality Control and Feedback Systems:
Many modern CNC lathes are equipped with sensors and feedback systems that monitor the machining process in real-time. These systems can detect any deviations from the programmed specifications and make immediate adjustments to correct the issue. For example, if a tool starts to wear down, the machine can automatically adjust the feed rate or cutting depth to compensate for the wear, ensuring that the part remains within the desired tolerance. This real-time monitoring and correction help maintain high levels of precision throughout the production process.
Applications of Precision Lathe Machining
The enhanced precision of lathe machining has made it indispensable in a variety of industries:
Aerospace:
In aerospace manufacturing, components such as turbine blades, engine parts, and landing gear require precise dimensions and flawless surface finishes. Lathe machining ensures that these parts meet the exact specifications necessary for safe and efficient operation in high-stress environments.
Automotive:
In the automotive industry, lathe machining is used to produce engine components, transmission parts, and suspension systems. Precision is critical for ensuring the proper fit and function of these parts, as even a small deviation can lead to performance issues or mechanical failures.
Medical Devices:
Lathe machining plays a vital role in producing medical instruments, prosthetics, and implants, which require high levels of precision to function correctly within the human body. The ability to machine complex shapes with tight tolerances makes lathes ideal for this application.
Electronics:
In the electronics industry, lathe machining is used to produce components such as connectors, housings, and heat sinks. These parts must be manufactured with extreme accuracy to ensure proper assembly and function within electronic devices.
Conclusion
From CNC automation and multi-axis capabilities to advanced tooling materials and real-time feedback systems, lathe machining offers manufacturers the ability to produce components with tight tolerances and consistent quality. As industries continue to demand higher precision in their products, lathe machining will remain an essential process in the future of manufacturing, driving innovation and ensuring the reliability and performance of critical components.
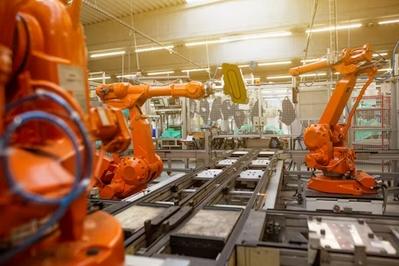